It is common knowledge that plastic injection molding is one of the best and most relevant machining processes in the machine industry. The plastic injection molding machine helps you produce products in high volume and record time. Before you consider buying a plastic injection molding machine, there are several factors, such as Shot Size, Tie Bar Spacing, Ejector Stroke, Platen Size, and Tonnage.
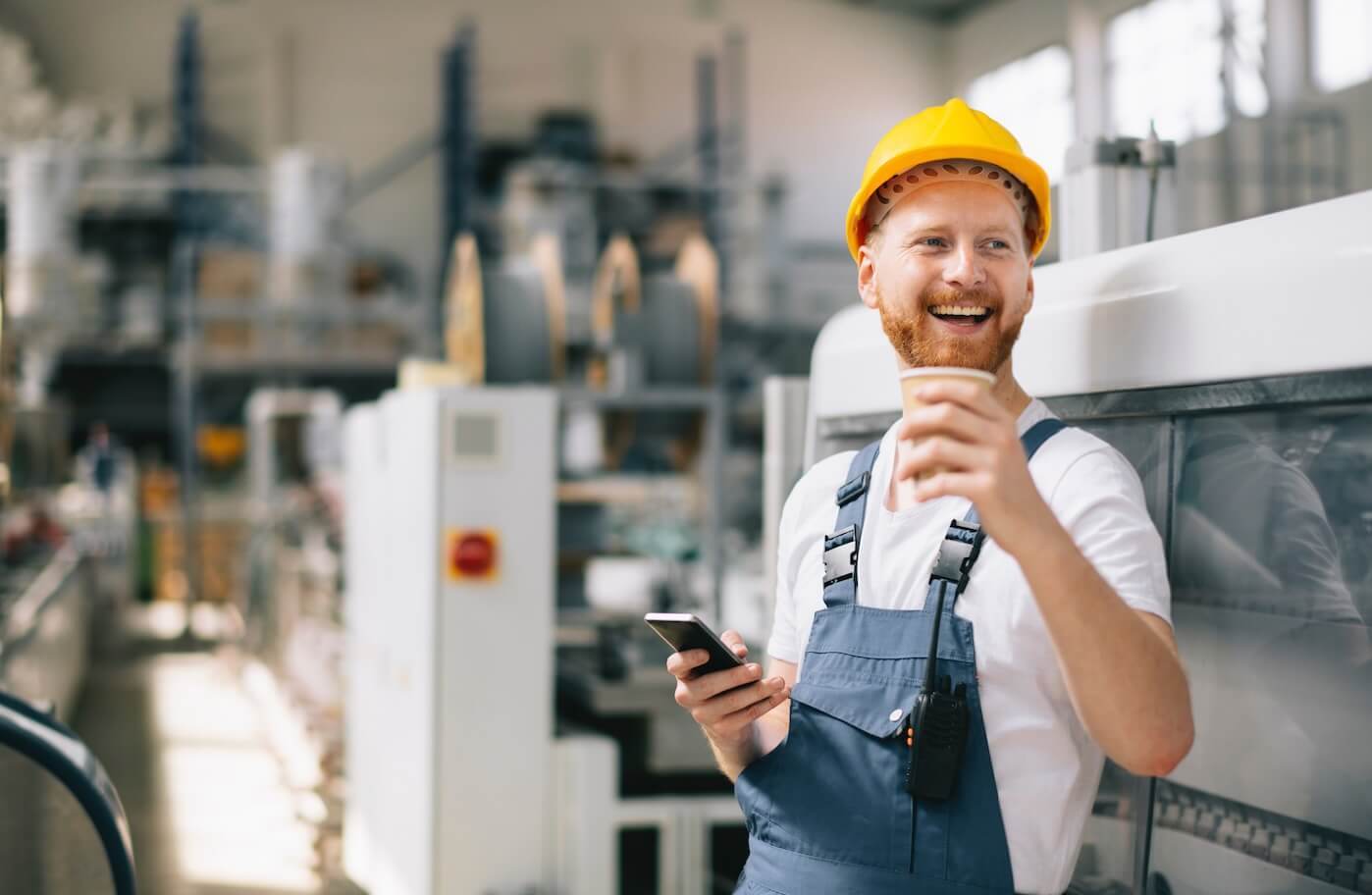
Each of these factors will be elaborated on in subsequent paragraphs below:
-
Shot Size
Shot size is the total amount of plastic the injection molding machine can inject into the molding cavity in one molding cycle. The amount can be calculated in ounces of “general purpose polystyrene” (GPPS) for U.S. machines and cm3 for European and Asian machines. If you don’t get the shot size right, you might buy a plastic injection molding machine that doesn’t fit your requirement. It’s always best to look for a machine that can produce 30-40% greater shot sizes that exceed the amount your product(parts) requires.
-
Tonnage
Tonnage here means clamp tonnage or clamping pressure. This process follows the concept of when you’re examining press brakes. With press brakes, the strength of the tonnage is measured by how securely the machine can direct tons of downforce toward a workpiece. However, with plastic injection molding machines, tonnage can be measured by the number of tons the device can press together with the plates to hold down the mold cavity so that the plastic injected into the cavity can solidify and take form.
-
Platen Size
The platen is the tool or table where the mold cavity is installed. The platen is divided for the mold to be inserted and fastened securely to the platens. Once the two platens are joined together and are held down under the weight of the tonnage, the plastic is heated, injected under pressure, and given some time to cool following a molding cooling cycle. Afterward, the plastic cools, solidifies, and takes shape while still being kept in place with many tonnes, so it doesn’t get out of the desired shape.
-
Tie Bar Spacing
The holes in the platen are designed for pins to go through it, ejecting molds. Tie bar spacing is the space between the horizontal tie bars on an injection molding machine. Hence, the measurement coupled with the platen max spacing will ascertain the biggest size of molds that the molding machine can hold.
-
Ejector Stroke
The ejector stroke is when the machine ejects the finished products from the platens using ejector pins. The ejector in the molding machine presses against an ejector plate on the mold; ejection pins are rods installed on the ejector plate and then push the molded parts after the plastic has solidified and the mold has opened.
After the molding process is completed, the mold opens, and the ejector slowly pushes the finished product out of the mold cavity. The pin movement works in tandem with mold opening because if the pin moves wrongly, it affects the finished product.