The advent of Industry 4.0 has revolutionized the way we perceive manufacturing operations, heralding an era characterized by an unprecedented level of automation and connectivity. A pivotal component of this transformation is the integration of connected sensor technology in factories.
These sensors have redefined machine perception by equipping machines with capabilities to sense, perceive, and interpret their surroundings in a way that significantly enhances productivity and efficiency.
The Advent of Connected Sensor Technology
Sensor technology has come a long way since its inception. Initially used to perform rudimentary tasks such as temperature monitoring or pressure sensing, sensor technology has now evolved to perform complex tasks that include vibration monitoring, predicting equipment failure, and even gauging product quality in real-time.
Connected sensor technology further amplifies the capabilities of these sensors by integrating them into the factory’s larger IoT (Internet of Things) network. This connected ecosystem facilitates real-time data collection, sharing, and analysis, enabling factories to be more agile, efficient, and proactive in their operations.
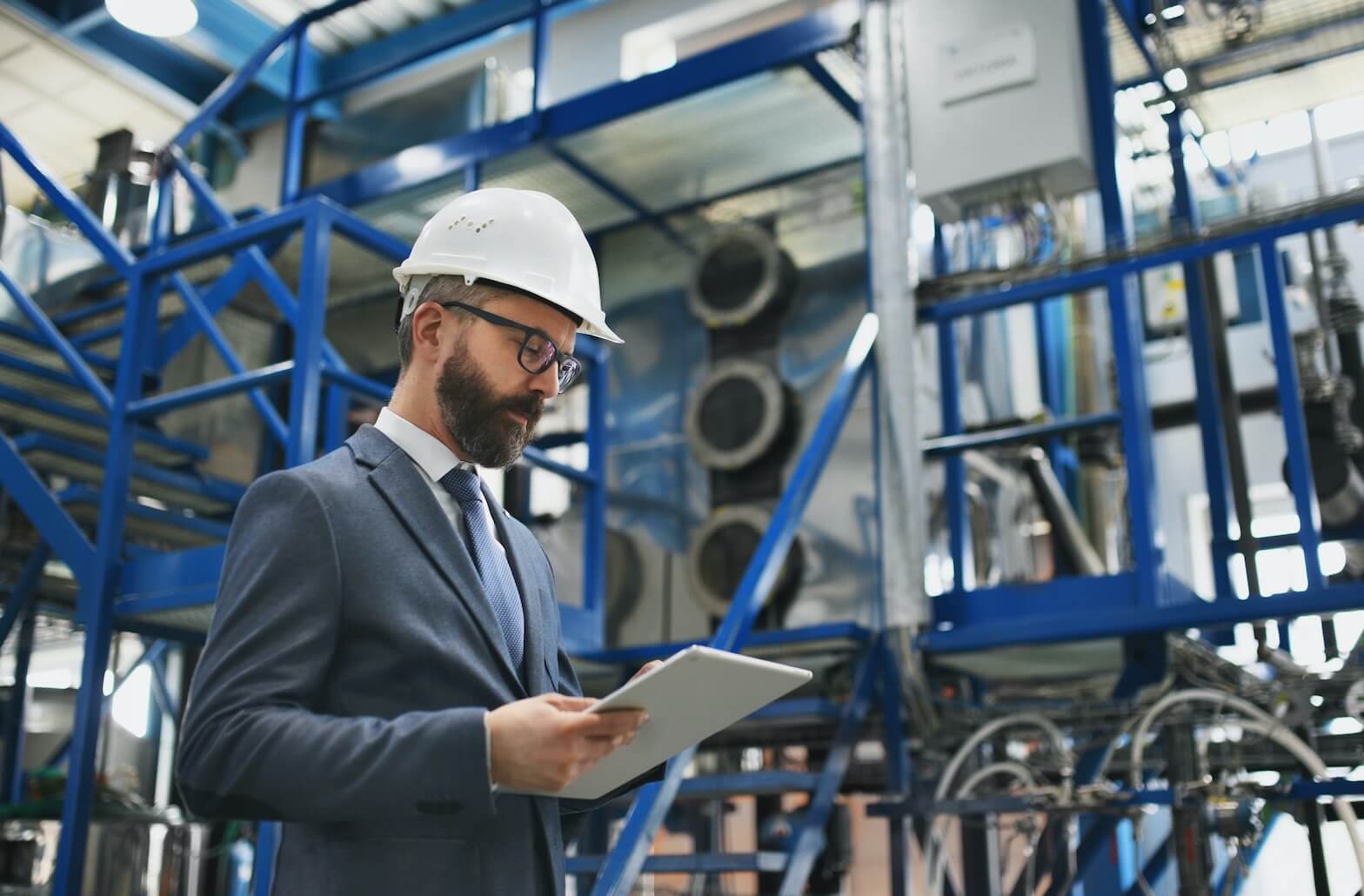
Redefining Machine Perception
Enhanced Sensory Capabilities
Machine perception has traditionally been limited to the tasks that machines were explicitly programmed to perform. Connected sensor technology, however, is changing this narrative.
Sensors not only provide machines with the ability to detect and respond to changes in their environment, but they also enable machines to perceive and analyze these changes in a context-aware manner. This enhanced perception opens up new opportunities for machines to learn from their environment and make data-driven decisions, thereby driving greater operational efficiency.
Predictive Analysis and Maintenance
Connected sensor technology is also redefining machine perception through predictive analysis. By monitoring operational parameters and detecting anomalies, sensors can identify patterns indicative of impending equipment failures.
With the additional capability of machine learning algorithms, these patterns can be analyzed and interpreted using the benefits of continuous vibration monitor to predict equipment breakdowns before they happen. As a result, predictive maintenance replaces traditional reactive maintenance, reducing downtime and increasing overall operational efficiency.
Quality Control and Assurance
The sensor-enabled machine perception revolution is also making strides in the realm of quality control and assurance.
With the help of advanced sensor technologies such as machine vision, factories are now able to carry out real-time inspection and quality assurance of products. This not only increases the speed of the manufacturing process but also reduces the chances of defective products reaching the market.
The Connected Factory: A Symbiotic Ecosystem
At the heart of this paradigm shift is the connected factory – a symbiotic ecosystem where machines, sensors, and humans coexist. In this ecosystem, connected sensors provide machines with a perception that closely resembles human senses, enabling them to understand and respond to their environment in real-time.
Machines, equipped with these sensor-driven perceptions, are better equipped to collaborate with humans, making factories safer and more efficient. Workers can focus on high-level tasks, while machines handle repetitive, strenuous, and precision-demanding operations. This optimizes productivity, enhances product quality, and improves working conditions.
The Critical Link in a Connected Factory
In this equation of factory productivity and efficiency, the role of components such as sensor cables cannot be overstated. These cables are essential as they form the physical backbone that connect sensors with the machines and the larger industrial network.
Sensor cables are the vital channels that transport critical data from the sensors to the machines and to the control systems. This data, often in real-time, includes information about operational conditions, anomalies, environmental factors, and more. Without these cables, it would be impossible for the sensors to communicate the data that allows machines to ‘perceive’ their surroundings and act accordingly.
Murrelektronik Inc. is a prominent component supplier that stands out in the market with one of the largest varieties of high-quality cables. Murreletronik’s sensor and actuator cables are specifically designed to ensure efficient and reliable data transmission, thereby enabling an industrial ecosystem where machines can make informed decisions based on accurate, real-time data.
The Future of Connected Sensor Technology in Factories
The potential of connected sensor technology in factories is vast and still unfolding. The future will witness the rise of smarter factories with machines that have an advanced level of perception and autonomous decision-making capabilities.
From predictive maintenance to real-time quality control, from energy efficiency to improved safety, the impact of connected sensor technology in redefining machine perception is profound. As we continue to explore and harness the power of this technology, the factories of the future will be characterized by their adaptability, resilience, and efficiency.
The Transformative Power of Connected Sensor Technology
The marriage of machine perception and connected sensor technology is a testament to the incredible strides we’ve made in the realm of industrial automation. It provides us with a glimpse into the future – a future where smart factories will redefine the manufacturing landscape, driving unprecedented levels of efficiency, productivity, and quality.
As the capabilities of connected sensor technology continue to evolve, so too will the perception and intelligence of machines, heralding a new era in manufacturing operations. This transformative journey, led by connected sensor technology, is not just about building smarter machines; it’s about building smarter factories and, in essence, a smarter world.
Indeed, connected sensor technology is redefining machine perception, and in doing so, it’s redefining the future of manufacturing.