In today’s fast-paced business environment, detecting and preventing product defects is crucial to maintaining a competitive edge. An effective inspection system is critical to achieving this goal. However, choosing the right tool can be challenging. With so many options available, it can take time to determine which one is the best fit for your business.Â
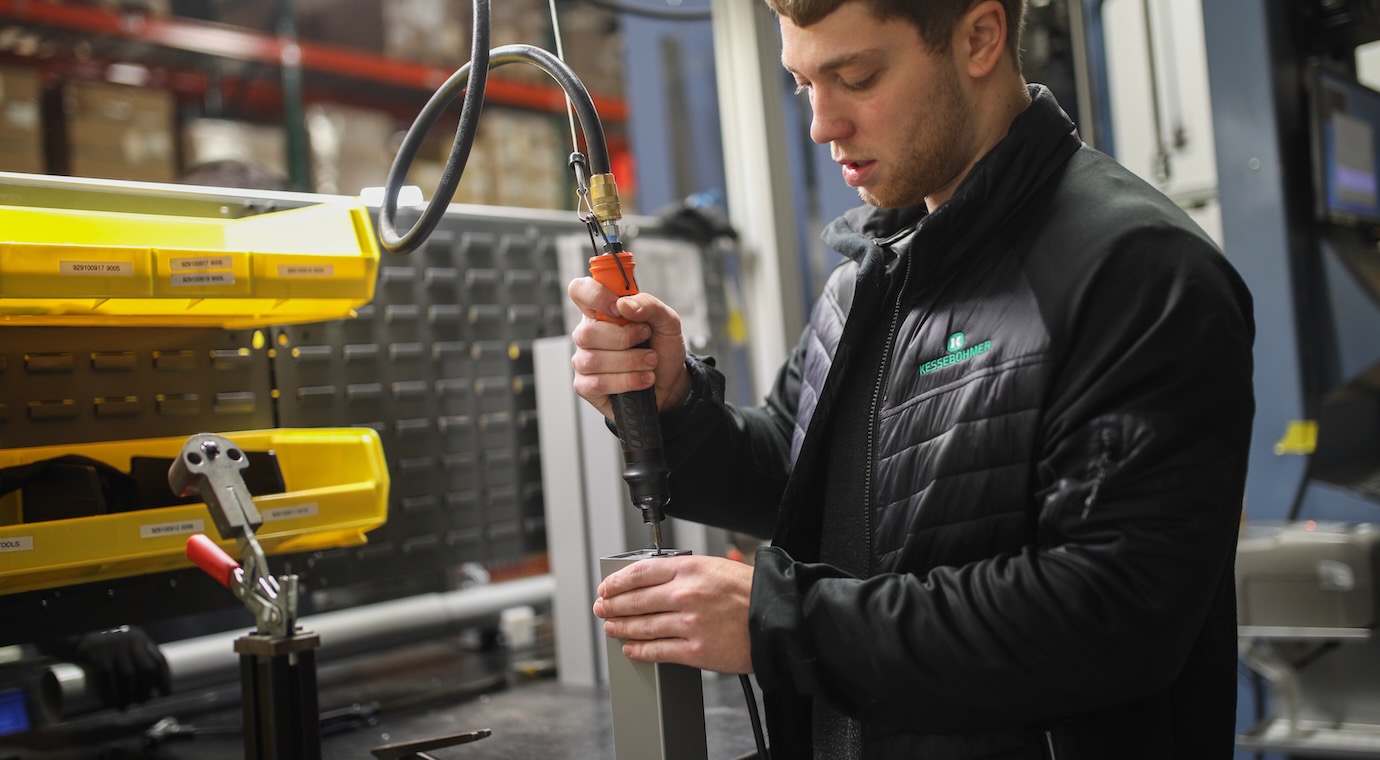
Here are vital factors to consider when choosing the right inspection system for your business:
1. Work With A Reputable Manufacturer
Look for reviews and testimonials from other customers who’ve purchased and used your prospective inspection system. Additionally, you should check the manufacturer’s reputation and history in the industry.
Look for TDI Packsys and similar companies with a track record of delivering quality inspection systems and providing excellent customer support. By choosing a reputable manufacturer, you can be confident you’re investing in a high-quality product that’ll bring reliable results. Furthermore, such companies ensure that any issues with the inspection system are promptly resolved, minimizing downtime and ensuring that production runs smoothly.
2. Identify Your Inspection Needs
Another important step in choosing the right inspection system for your business is identifying your inspection needs. This involves determining the type of inspection you need, the items you need to inspect, and the criteria you want to use. You should also consider the speed and accuracy required. Below is a detailed discussion of these factors.
- Type of inspection: The type of inspection required depends on the product being produced. For example, in the food industry, inspections may involve detecting foreign objects, such as metal or glass. In contrast, in the pharmaceutical industry, inspections may involve identifying the presence of a specific chemical compound.Â
- Items to inspect: The items to inspect depend on the specific product being produced. For example, in the food industry, inspections may involve checking the weight of products, while in the automotive industry, inspections may involve checking the dimensions of parts.
- Criteria to use: The criteria to use for inspection may vary depending on the product and industry. For example, in the food industry, criteria may involve checking for allergens or ensuring that the product meets specific nutritional requirements.
- Required speed and accuracy: The required speed and accuracy of the inspection system depend on the production rate and the level of precision required. For example, high-speed production lines require inspection systems to keep up with the production rate, while precision manufacturing requires inspection systems that detect even minor defects.
Once you’ve identified your inspection needs, you can evaluate the available systems and select the most appropriate one for your business. This ensures that you invest in an inspection system that meets your specific requirements, improving your products’ quality and safety while boosting your business’s efficiency and productivity.
3. Research The Available Inspection Systems
The next step is to research the available inspection systems that meet your requirements. This involves evaluating the technology used, the cost, and the features of each system.
When evaluating the technology used in an inspection system, consider the level of automation and its ability to integrate with other systems. You should also assess the speed and accuracy of the system to ensure that it meets your requirements.
Cost is also an important consideration when choosing an inspection system. While some systems may have a higher upfront cost, they may be more cost-effective in the long run due to lower maintenance and operating costs. You should also consider the system’s return on investment (ROI) to ensure it’s worthwhile for your business.
Finally, consider the features of the inspection system, such as the ability to handle different types of products, the ease of use, and the level of customization available. You can determine which inspection system best suits your business by evaluating these aspects.
Different inspection systems are available, each having its strengths and weaknesses. These include:
- Vision inspection systems: These use cameras and image processing software to identify product defects.
- X-ray inspection systems: These use X-rays to detect defects in products that aren’t visible to the naked eye.
- Metal detection systems: These use electromagnetic fields to detect metal contaminants in products.
- Checkweigher systems: These measure the weight of products to ensure that they meet the specified weight requirements.
By identifying your inspection needs, you can narrow down the options and focus on the best-suited inspection systems for your business.Â
4. Consider Compatibility And Integration
The inspection system you choose should be compatible with your existing systems and equipment to provide accurate and timely results and avoid disruptions or delays. Compatibility issues can lead to delays in production and reduced efficiency. Additionally, these problems may require significant modifications to your production line, which can be costly and time-consuming.Â
Moreover, integrating an inspection system with your existing systems and equipment ensures seamless operations and productivity. One important integration aspect is the availability of a software development kit (SDK). It allows developers to integrate the inspection system with other software systems. Choosing an inspection system with an SDK can simplify the integration process and reduce the chances of compatibility issues.
In addition, it’s important to consider interoperability when choosing an inspection system. This way, you can ensure that it’s able to work perfectly with your business’s implements, including production equipment, software systems, and databases. This helps ensure data flow seamlessly across all applications, improving accuracy and efficiency.
5. Test The System
Once you’ve identified a few potential inspection systems, testing them in your business environment is essential. This will help you evaluate the system’s performance and determine whether it meets your requirements. It’ll also help you identify potential issues or limitations.
During the testing phase, you should evaluate the speed and accuracy of the system, as well as its ability to handle different types of products. Also, consider the ease of use and the level of customization available.Â
6. Consider The Training And Support
You should check whether the manufacturer provides training and support for the inspection system. Additionally, you should ensure that your staff is trained to operate the system. This will ensure that your staff can use it effectively, minimizing the risk of errors and maximizing efficiency. Furthermore, good customer support will ensure that any issues with the inspection system are promptly resolved, minimizing downtime.
Conclusion
Choosing the right inspection system for your business requires careful consideration of various factors. By identifying your inspection needs, researching available options, evaluating compatibility, assessing the manufacturer’s reputation, considering the cost, and testing the system, you can decide which inspection system best suits your business.