Keeping aircraft in the air and generating revenue requires diligent maintenance programs. With airlines operating on slim profit margins, every minute an aircraft spends on the ground instead of flying equates to lost income.Â
As fleet managers, you must implement robust maintenance protocols focused on preventative care rather than fixing issues as they arise. Doing so enables you to maximize your fleet’s uptime while ensuring passenger safety never gets compromised.
To achieve best-in-class aircraft uptime of over 99%, you need consistent inspections and a steadfast commitment to maintenance schedules. Also, having top-tier equipment to refuel aircrafts and qualified technicians simplifies the upkeep processes to attain high utilization rates.
This article explores tips on how an unwavering dedication to maintenance helps optimize aircraft uptime.
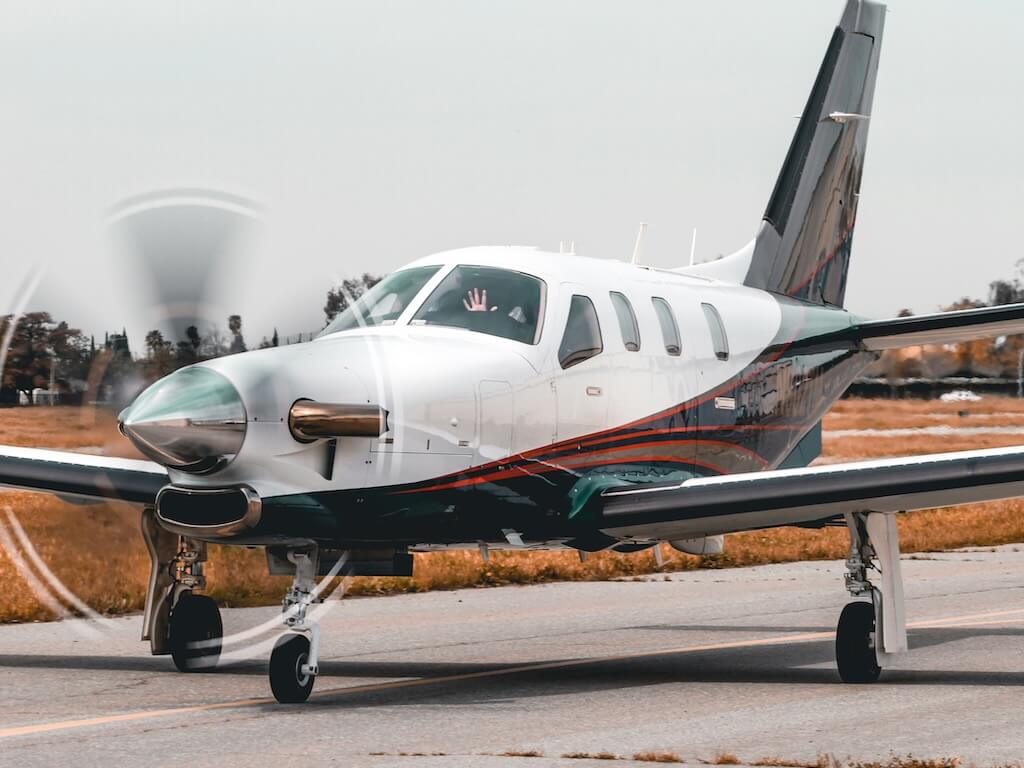
Implement Inspection Programs
Developing aircraft inspection protocols aligned to usage metrics instead of the calendar provides better uptime returns. You don’t want to take an aircraft with low monthly flight hours out of service for an invasive check when it isn’t necessary.Â
On the other hand, heavily utilized planes need more frequent and rigorous examinations to spot issues in their infancy. This allows for minor repairs instead of major overhauls after problems escalate.
Also, you should break inspection checklists into three main areas—interior, exterior, and system—and segment each section into zones. For example, zone exterior inspections into the nose, wings, engines, aft fuselage, landing gear, etc.Â
System checks get separated into categories like electrical, hydraulics, pressurization, etc. This zoning methodology enables technicians to thoroughly scrutinize every inch of an aircraft systematically.Â
During examinations, technicians inspect each zone independently, sign off after verification, and move to the next area. Such an approach guarantees no sections get overlooked when performing aircraft inspections.Â
Standardize On Routine Maintenance Intervals
While aircraft come with manufacturer guidance on component maximum usage intervals, you should implement maintenance plans around shorter cycles. For example, landing gear manufacturers may indicate wheels and brakes as needing replacements every 1,500 cycles. But to prevent failures due to worn parts, replacing them every 1,000 cycles reduces the chances of problematic issues arising.
The key is determining what interval timing delivers the optimal balance between performance, safety, and cost. If doing repairs every 500 cycles generates little incremental value over 1,000 cycles but doubles expenses, it likely makes sense to use the longer replacement interval.Â
On the other hand, doubling intervals to save money when it considerably raises safety risks proves foolish. Working with OEMs and reviewing internal data helps decide appropriate cycles for component swaps.
Additionally, specific parts like oil and air filters degrade not necessarily due to use but rather the passage of time. For these routine consumables critical to smooth engine operations, calendar intervals take precedence over usage metrics. Unless filters get physically damaged, replacing them based on engine hours alone often leaves excess useful life still available.Â
Always Have Qualified Aircraft Mechanics Available
Implementing meticulous maintenance programs provides no aviation uptime improvements unless you have technicians to conduct repairs skillfully and quickly.Â
When aircraft break, having qualified mechanics available 24/7 to troubleshoot issues minimizes downtime. While some problems require taking planes out of service for multiple days, many minor repairs prove executable overnight or even in a few hours. But such rapid turnarounds only happen with mechanics continually on standby capable of addressing issues.Â
Though keeping skilled technicians always available proves expensive, the payback from higher fleet utilization outweighs the incremental staffing costs.Â
Supplement In-House Talent With Trusted Partners
Despite large investments in mechanic training and broad capabilities, situations arise that hamper your team’s capacity to fix issues rapidly.Â
Severe weather disruptions and unexpected fleet reliability challenges can overwhelm internal maintenance capacity quickly. Augment in-house capabilities via contracts with specialized MRO providers helps alleviate resource constraints preventing aircraft from returning to service swiftly.
The key is only partnering with MROs possessing demonstrated competencies in maintaining precise aircraft fleet types. With extensive aviation MRO experience under their belts, quality vendors can dispatch technicians immediately with the expertise to troubleshoot and fix problems without delays regular staff shortfalls might cause.Â
Keeping planes moving by accessing supplemental maintenance support allows for maximizing fleet availability despite unforeseen events straining your technical team.Â
Final Thoughts
With thin margins and high costs, optimizing aircraft uptime required achieving profitability. However, emphasizing fleet availability means little without maintaining unwavering passenger safety standards. Balancing maximization uptime goals with strong reliability metrics ultimately enables stable airline performance over the long run.
By implementing these strategies, aviation managers keep their fleets in peak operating condition. Combined with sound governance and continual program enhancements, such an approach leads the way toward best-in-class fleet utilization.